DIN 2093 Шайба пружина тарельчатая HENNLICH
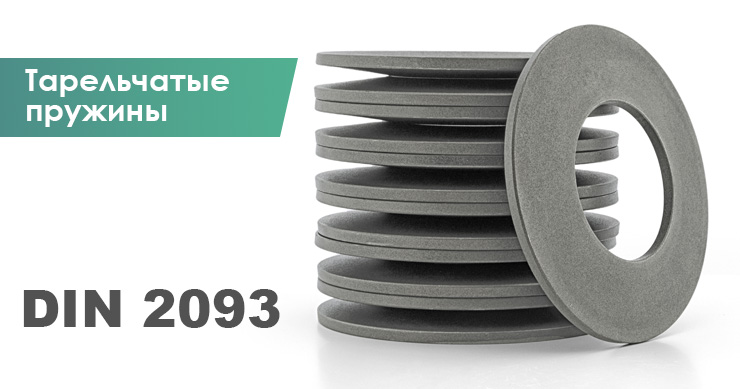
1. Сфера и область применения
2. Определение
3. Символы и единицы измерения
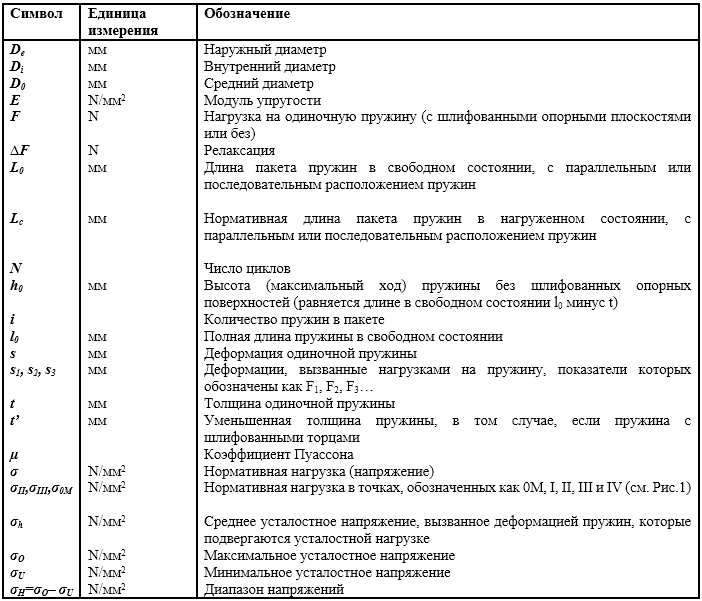
4. Классификация
Группа |
Толщина одиночной пружины, t |
Одиночная пружина со шлифованными торцами |
---|---|---|
1 |
Меньше чем 1,25 |
Нет |
2 |
От 1,25 до 6 |
Нет |
3 |
От 6 до 14 |
Да |
5. Размеры и обозначения
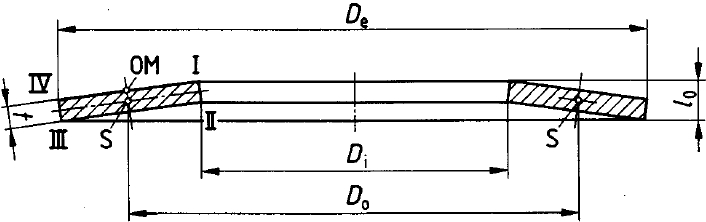
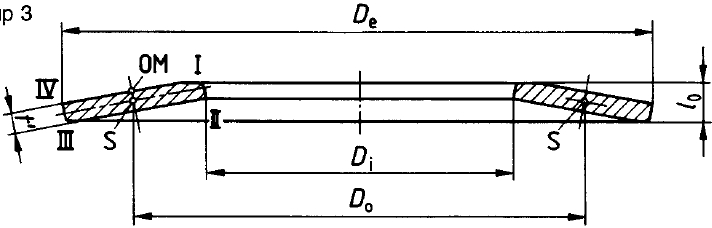
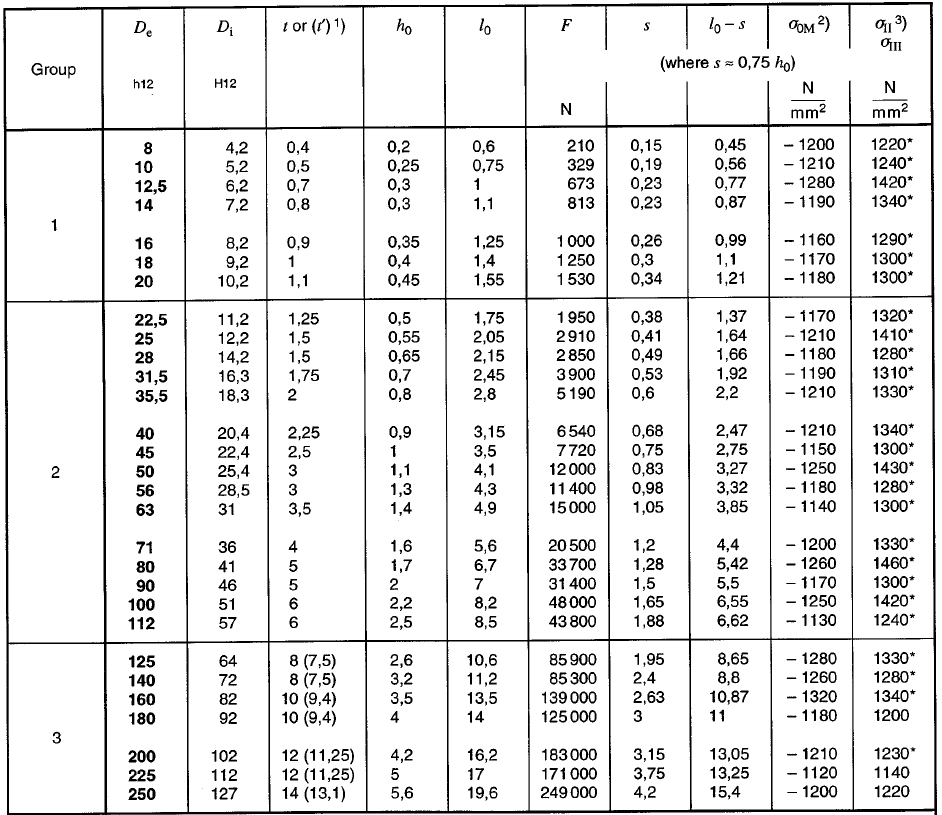
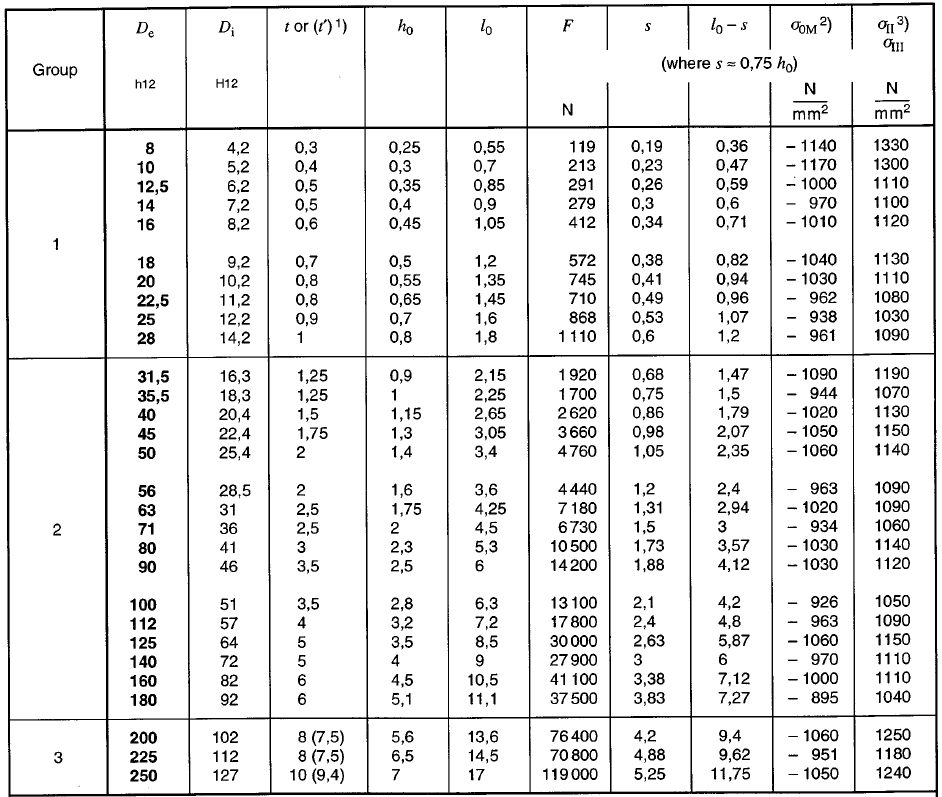
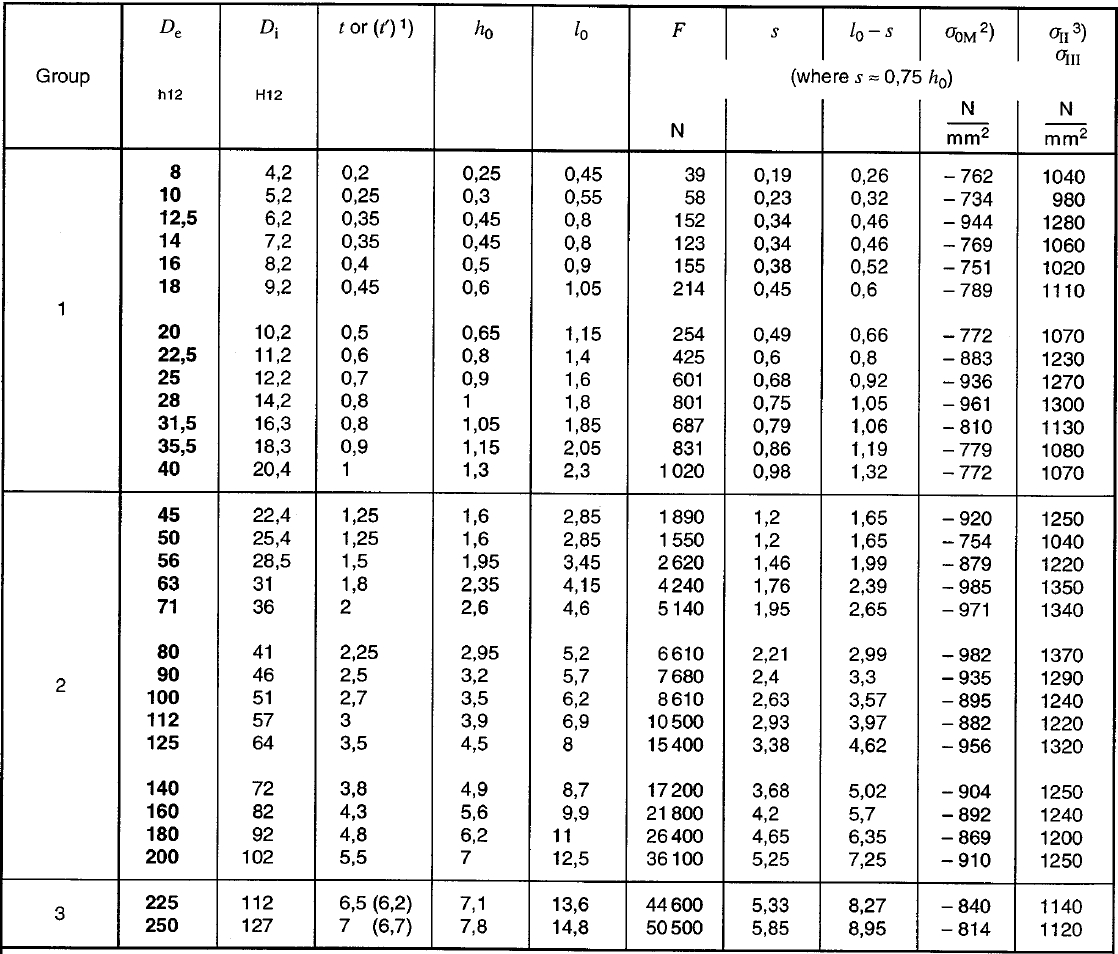
В том случае, если используются пружины с шлифованными торцами (см. группу 3 в пункте 4), заданную нагрузку на пружину F (где s приблизительно равно 0,75 h0), можно получить путём уменьшения толщины одиночной пружины t, что в результате даст значение t’. Если используются пружины серии А и В, значение t’ должно быть приблизительно равно 0,94t, а в случае использования пружин серии С, t’ должно быть приблизительно равно 0,96t.
6. Допуски тарельчатых пружин
Группа |
t или t’ |
Предельные отклонения 4) |
1
|
От 0,2 до 0,6 |
+ 0,02 |
От 0,6 до 1,25 |
+ 0,03 |
|
2 |
От 1,25 до 3,8 |
+ 0,04 |
От 3,8 до 6,0 |
+ 0,05 |
|
3 |
От 6,0 до 14, 0 |
± 0,10 |
4) Для 3 группы пружин, указанные предельные отклонения применяются к уменьшенной толщине t' (см. пункт 4 и 5). |
6.3. Допуск на высоту пружины в свободном состоянии, lo
Группа |
t |
Предельные отклонения |
1 |
Меньше чем 1,25 |
+ 0,10 |
2 |
От 1,25 до 2,0 |
+ 0,15 |
От 2,0 до 3,0 |
+ 0,20 |
|
От 3,0 до 6,0 |
+ 0,30 |
|
3 |
От 6,0 до 14,0 |
± 0,30 |
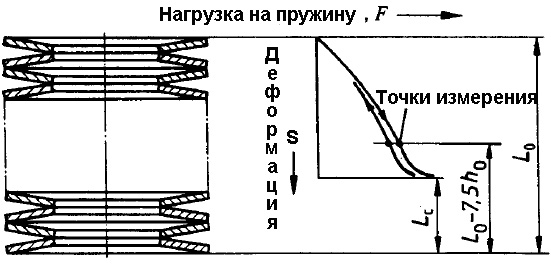
7. Допуски на нагрузку тарельчатых пружин
Группа |
t |
Предельные отклонения для F, при l0 – 0,75 h0 в процентном соотношении |
1 |
Меньше чем 1,25 |
+ 25 |
2 |
От 1,25 до 3,0 |
+ 15 |
От 3,0 до 6,0 |
+ 10 |
|
3 |
От 6,0 до 14,0 |
± 5 |
7.2. Пакеты тарельчатых пружин с последовательным расположением.
Группа |
Минимальная нагрузка на пружину (кривая разгрузки) в процентах, для пружин серий |
||
А |
В |
С |
|
1 |
90 |
85 |
|
2 |
92,5 |
87,5 |
|
3 |
95 |
90 |
8. Зазор между тарельчатой пружиной и центрирующим элементом
Di или De |
Примерная величина зазора |
До 16 |
0,2 |
От 16 до 20 |
0,3 |
От 20 до 26 |
0,4 |
От 26 до 31,5 |
0,5 |
От 31,5 до 50 |
0,6 |
От 50 до 80 |
0,8 |
От 80 до 140 |
1 |
От 140 до 250 |
1,6 |
9. Допустимая осадка тарельчатых пружин
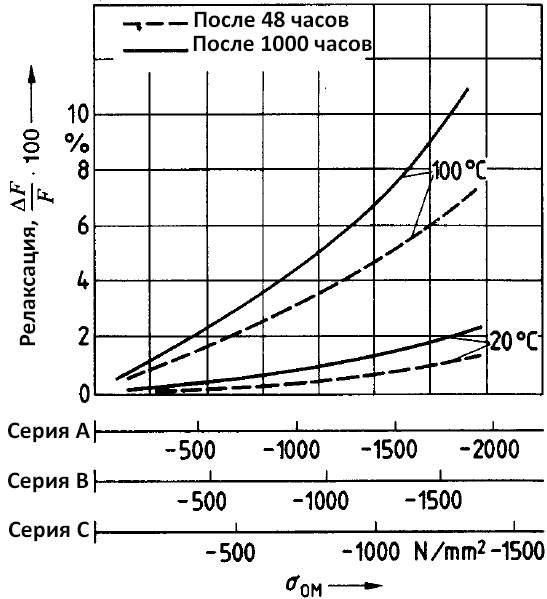
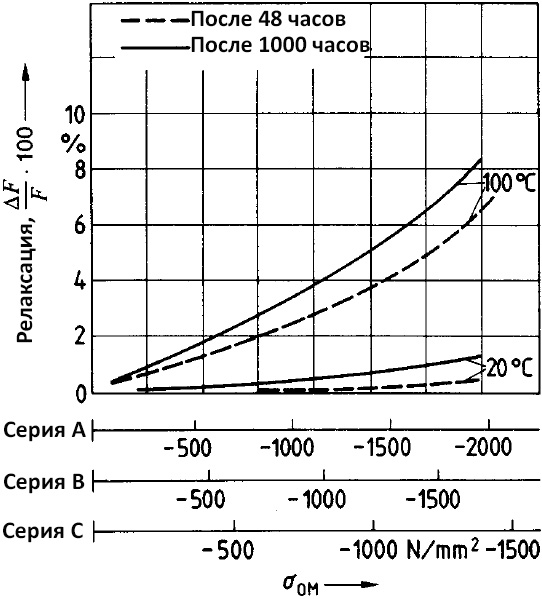
10. Точки напряжения в пружинах, которые подвергаются воздействию статической нагрузки или же умеренной усталостной нагрузки
11. Точки напряжения в тарельчатых пружинах, которые подвергаются воздействию усталостной нагрузки
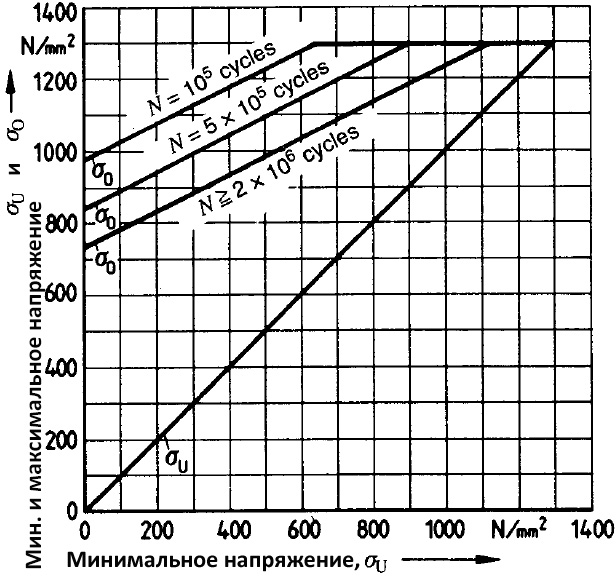
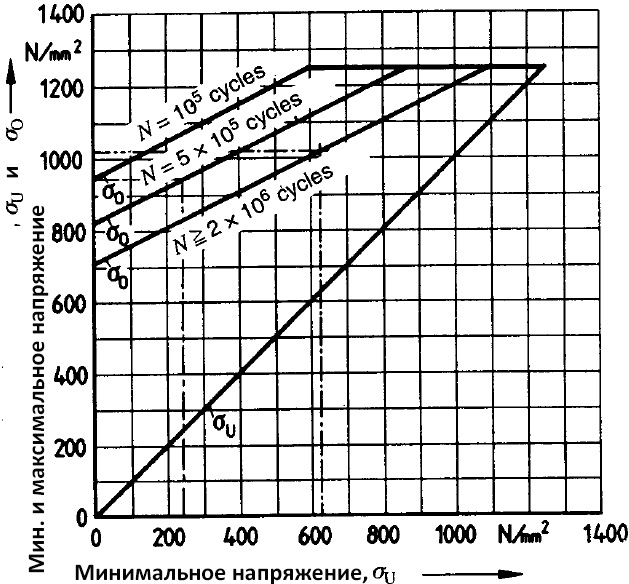
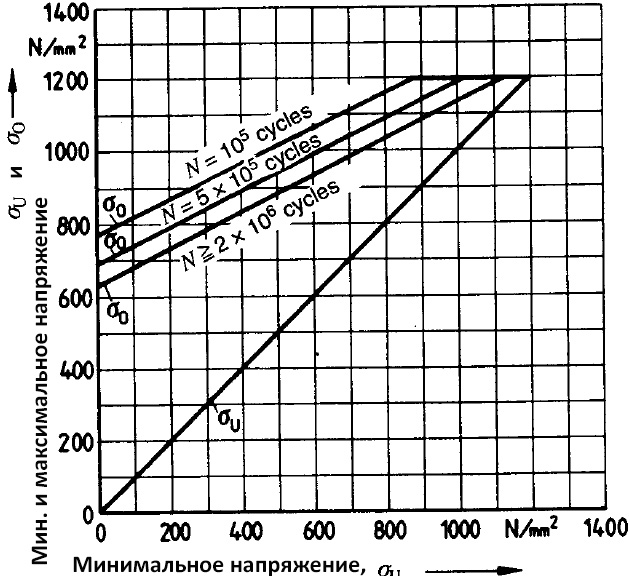
12. Виды используемых материалов
13. Процесс производства тарельчатых пружин и качество обработки поверхности
Группа |
Процесс производства |
Шероховатость поверхности**) в μm на |
|
Верхней и нижней поверхности |
Наружной и внутренней поверхности |
||
1 |
Токарная обработка, холодная формовка, скруглённые кромки |
Ra < 3,2 |
Ra < 12,5 |
2 *) |
Токарная обработка, холодная формовка, точёные наружный и внутренний диаметры De и Di, скруглённые кромки |
Ra < 6,3 |
Ra < 6,3 |
Токарная обработка, холодная формовка, скруглённые кромки |
Ra < 6,3 |
Ra < 3,2 |
|
3 |
Холодная или горячая формовка, все стороны точёные, скруглённые кромки |
Ra < 12,5 |
Ra < 12,5 |
*) Если нет иных указаний использование специальных процессов производства зависит от решения производителя (см. пункт 5). **) Указанные значения не могут применяться к уплотнениям, которые прошли обработку дробеструйным упрочнением. |
14. Закалка и обработка поверхности
15. Испытание тарельчатых пружин
Характеристики пружин |
AQL Значение |
Основные характеристики Нагрузка на пружину F (где s примерно равно 0,75 h0) Наружный диаметр De Внутренний диаметр Di |
1 |
Менее значимые характеристики Полная длина пружины в свободном состоянии l0 Толщина пружины t или t’ Шершавость поверхности Ra |
1,5 |
6.1.Испытания пружин на прочность
Метод измерения твердости металла по Роквеллу должен применяться как описано в Части 1 DIN 50 103, а метод измерения твердости металла по Виккерсу (для 1 группы пружин) как описано в DIN 50 133. Вдавливание должно выполняться на верхней поверхности пружины, в точке, которая расположена по центру между внешним и внутренним краем.
7.Прочие требования
В тех случаях, если это возможно, центрирующий элемент и посадочное место должны быть изготовлены из упрочнённых материалов, с глубиной обезуглероженного слоя примерно 0,8 мм и твердостью 55 HRC. Поверхность центрирующего элемента должна быть гладкой и, если это необходимо, отполированной.
В тех случаях, когда пружина подвергается статической нагрузке, разрешается использовать незакалённые центрирующие элементы.
Стандарты, ссылки на которые присутствуют в тексте
DIN 267 Часть 5 DIN 1777 DIN 2092 DIN 6796 DIN 17 221 DIN 17 222 DIN 17 224 DIN 50 103 Часть 1 DIN 50 133
DIN 50 969 |
Крепежные элементы; технические условия поставки; приёмочный контроль (дополненная версия ISO 3269:1984) Пластичные медные сплавы для пружин; технические условия поставки Проектирование конических тарельчатых пружин Тарельчатые пружинные шайбы для узлов с гайками/болтами Горячекатаная сталь для пружин; технические условия поставки Холоднокатаная сталь; технические условия поставки Нержавеющая проволока и сталь; технические условия поставки Метод измерения твердости по Роквеллу; шкалы С, A, B, F Метод измерения твердости по Виккерсу; HV 0,2 – HV 100 Закалка химически обработанных и/или гальванизированных высокопрочных стальных элементов для предотвращения водородной хрупкости |
Другие значимые стандарты
DIN 1016 DIN 1544 DIN 8201 Часть 1 DIN 50 942 DIN 59 200
|
Горячекатаные стальные листы и полосы; допуски на размер, форму и вес Стальные листовые прокаты; холоднокатаные стальные полосы; размеры, предельные отклонения и допуски на формы Абразивные материалы; классификация и обозначения Фосфатирование металлов; методы тестирования Горячекатаные широкие листовые прокаты; размеры и допуски на размер, форму и вес |
Предыдущие издания
DIN 2093; 05.57, 04.67, 04.78, 09.90.
Правки и Дополнения
В сравнении с изданием, вышедшим в Сентябре 1990 года, были внесены следующие правки:
- В Таблице 4, было исправлено значение, указанное для Di, где Dе равняется 50.
- В Таблице 5, было скорректировано предельное отклонение, указанное для 2 группы пружин.